Поездка на новый завод Britax Roemer
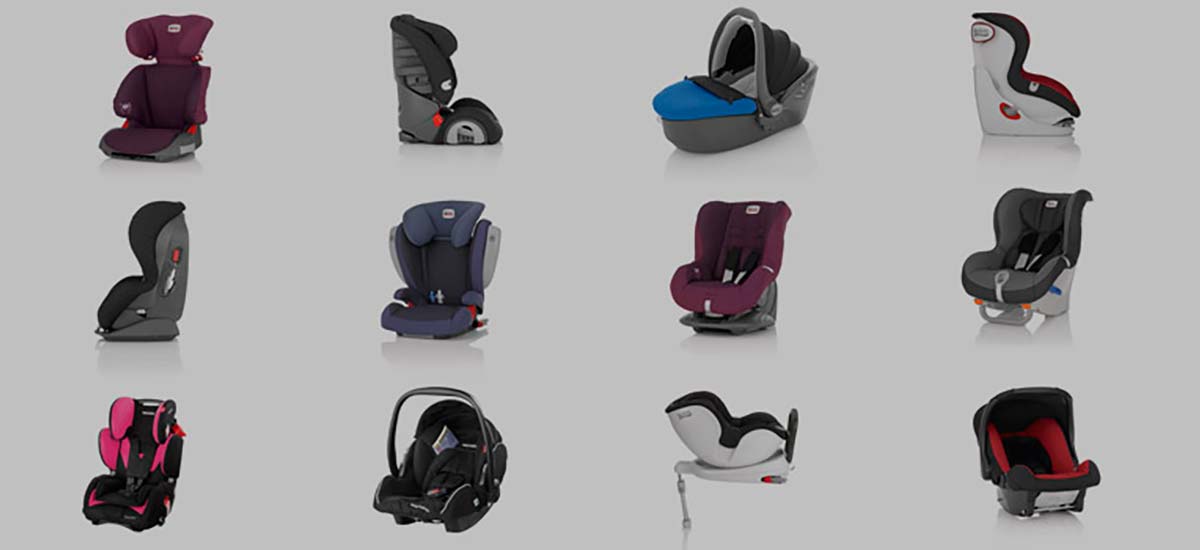
В начале апреля по приглашению наших немецких партнеров отправились в путешествие на новый завод известного производителя автокресел для детей Britax Roemer. Свое посещение предыдущего завода я описывал в статье несколько лет назад. Но теперь все по новому.
За это время компания спроектировала и построила с 0 в чистом поле новый современный завод. Находится он в г. Лайпхайм, примерно в 40 км от Ульма, где производство располагалось ранее.
Прибыли мы в аэропорт Мюнхена, откуда отправились в Ульм. Это такой симпатичный город на берегу Дуная с населением ~120 тыс человек, безумно спокойный и размеренный, немноголюдный. Симпатичная архитектура (самым выбивающимся из общего ряда зданием был наш отель), везде фигурки воробьев (символ города), в небольшой речке в центре плавает форель. В городе расположен самый высокий католический собор в Германии, на 4 метра выше второго по высоте - Кёльнского. Особенно интересно видеть совсем рядом с этим гигантом маленький русский православный храм.
В Лайпхайм мы отправились на следующее утро. Это совсем маленький промышленный городок с населением порядка 7 тыс. человек. Завод не то чтобы огромный, но очень современный.
Началось наше посещение с демонстрационного зала. На стене - фотографии продукции, которую Britax Roemer выпустила последние 50 лет. Особенно интересно изображение 1997 года модели кресла со столиком и изофикс ). Все же все новое - хорошо забытое старое, а ведь сейчас все эти технологии ассоциируются с совершенно другими брендами.
Далее расположен шоу-рум с современной продукцией концерна. Правда все выставленные новые цвета выкладывать запретили, т.к. они будут официально показаны только осенью, а все остальное и у нас в магазинах можно видеть.
После небольшого рассказа о том, как создавался новый завод, как было построено здание в чистом поле и как десятки лет опыта компании воплотились в проектировании, мы отправились непосредственно на производство.
Немного цифр.
На сегодняшний день на заводе производится в среднем 17000 детских кресел в неделю. В пиковые месяцы производство переводится в 2 смены, привлекается временный персонал и объем продукции увеличивается вдвое. Вся сборка производится полностью из местных комплектующих. Запасов практически нет, реализована система "точно вовремя" и все поступает ровно в тех количествах, в которых заказано. Если закрыть ворота завода, то все запасы комплектующих закончатся за пол дня. Соответственно, ни о каких приходящих машинах с какими-либо элементами из Китая сейчас тут и речи идти не может. Все крупные и дешевые узлы, например, пластик, производятся в пределах радиуса 40-50 км, а тяжелые и дорогие (например, элементы Isofix) - в пределах 600 км.
Вся зона производства вместе с зоной хранения умещается на ~10000 м2, и обслуживается всего лишь ~400 человек постоянного персонала.
Сборочный конвейер реализован по какой-то новой модной японской методике, когда сборка производятся отдельными ячейками из нескольких рабочих мест, на каждой из которых может быть произведена любая модель, и проблема на любом из участков не останавливает весь процесс. При этом сборка производится не помодельно (1000 кингов, 1500 кидфиксов и т.д.), а ровно в количестве и порядке поступающих заказов. Информация по каждой ячейке видна самим сотрудникам и выводится на контроль, где видна скорость работы и достигнутые результаты. Все четко, слаженно и кажется, что никто тут особо не торопится при всем притом.
Собранная продукция поступает в складскую часть здания. Здесь все сортируется по 4 этажам зоны хранения, все также с соблюдением порядка заказов. Принцип работы до конца не понял, но направляющие зоны хранения могут наклонятся, и при установке новой партии, предыдущая уже едет дальше, попадая в конце пути на конвеерную ленту, где опять же сортируется в соответствии с порядком заказов и перемещается уже к нужным воротам, откуда поедет дальше, в том числе, и в Россию.
В производственной зоне также расположена секция, которой по словам нашего гида, они особенно гордятся. Это место складирования брака, а гордятся ее скромными размерами. Сюда поступает брак со всего мира (хоть это и сложно сочетается с малыми размерами секции), все случаи тщательно изучаются, после чего часть продукции ремонтируется, часть сразу идет на замену.
После производства нас пригласили в испытательную лабораторию, где проводятся динамические испытания автокресел. Экскурсию возглавил Ричард, глава инженерной службы компании.
В лаборатории 2 катапульты. Правая - заботливо перенесенная с предыдущего завода. На ней производится весь цикл краш-тестов, как в любых режимах: ECE R44-04, ECE R129 (i-size), методике ADAC и т.д. Испытания проводятся на лобовой удар, боковой, боковой удар с проникновением, удар с перекрытием. На всем оборудовании стоят отметки, для простоты настроек под ту или иную систему тестирования.
Ричард долго демонстрировал нам стержни, через которые осуществляется торможение тележки и которые позволяют задать любую требуемую кривую торможения (на фото не они, а элемент, который вставляется между спиной манекена и кресла, чтобы имитировать ослабление ремешков). Причем, как выяснилось, на испытания сильно влияет практически все. Например, в предыдущем помещении не регулировалась в достаточной степени влажность воздуха и испытания нельзя было производить в дождь. Интересно, а во всех лабораториях, производящих краш-тесты учитывают влажность? )
Еще один важный момент, затрудняющий тесты - положение манекена в момент удара. Для того, чтобы объективно сравнивать различные модели или конструктивные решения между собой, необходимо добиться максимальной повторяемости эксперимента. Очевидно, что для удара на скорости 50 км/ч (ECE R44-04, лобовой) и тем более для удара на скорости 64 км/ч (лобовой в ADAC) сперва необходимо разогнать тележку. Но длина разгонной полосы не может быть безграничной. А значит, тележку разгоняют с серьезным ускорением и максимальной скорости она достигает как раз в момент удара. При этом, в процессе разгона, манекен имеет свойство непредсказуемо смещаться (да зачастую и вся конструкция), искажая результат. И чем короче катапульта, тем больше погрешность испытаний. Причем даже реалистичности такая ситуация не добавляет, поскольку в жизни соответствовала бы нажатию педали газа и максимальному ускорению непосредственно перед ударом (вместо попытки тормозить).
Собственно, именно в борьбе с этим явлением основная идея катапульты в левой части лаборатории. Вот это уже совершенно уникальная установка, разработанная и изготовленная непосредственно под заказ Britax Roemer. Суть ее в том, что все в процессе испытания происходит наоборот. Не тележка разгоняется по максимуму перед ударом о препятствие, а имитируется сам процесс удара. Так для фронтального теста кресло закреплено задом наперед, а мощная установка разгоняет тележку в точности соблюдая кривую непосредственно столкновения. Причем параметры установки позволяют достигать ускорения порядка 90g. Для сравнения, максимальная перегрузка при тестировании по правилам ECE R44-04 составляет "всего лишь" 28g.
Само помещение испытательной лаборатории проектировалось изначально под эту катапульту. Можно даже сказать, что оно построено вокруг нее. Хотя пол и кажется единым целым, но эта катапульта имеет независимый фундамент, не связанный с фундаментом здания, чтобы не передавались вибрации. С памятью проблемы, поэтому никак не могу вспомнить сколько там тысяч тонн бетона в ее основании, но цифра впечатляющая.
Но посмотреть на работу этого чуда мысли не удалось. В данный момент она проходит калибровку и должна приступить к реальным испытаниям где-то летом.
Кстати, обсудили с Ричардом, который является одним из авторов методики испытаний, заложенной в ECE R129 (i-size) особенности теста на боковой удар с проникновением. Я задал вопрос, который давно меня мучил, что новая методика, по сути является столь же односторонней, как и предыдущая. Если раньше мы били условно корпус автомобиля о стену, то кресло с манекеном начинало двигаться в сторону двери, и чем жестче оно было закреплено, тем меньше была инерция в момент его столкновения уже с дверью. И это правильно. Но проникновения не происходило.
Теперь все вроде как жестче, и проникновение происходит (непосредственное столкновение тарана условно бесконечной массы с креслом), причем на 16 см против среднестатистических 8-ми. Но с другой стороны, теперь начальная скорость столкновения всегда одинакова, поскольку нет промежуточного смещения кресла к двери (как и самой двери в этом типе испытания), таким образом, данный способ испытания несколько занижает результат жестко закрепленных (изофикс, донатяжители) кресел. Они не реализуют преимуществ жесткого крепления, при этом оно может ухудшать результат по сравнению с вариантом, когда кресло может свободно двигаться под действием тарана. Собственно предположение родилось из-за странных результатов, начиная с 2015 года, когда периодически кресла на изофикс стали получать оценки ниже таких же без него (особенно заметно на группе 0+ с базой и без).
По второй части все оказалось не так однозначно, т.к. в случае, если кресло начинает двигаться, то ограничены возможности его управляемой деформации, но в целом, Ричард согласился с тем, что теряются преимущества жесткого крепления при таком подходе.
В жизни имеет место совмещение обоих ситуаций (прежняя методика и нынешняя), поэтому в идеале лучшее кресло то, которое показывает достойный результат в обеих методиках. Но естественно, таких совмещенных испытаний проводить никто не будет, хотя бы потому, что очень дорого.
С другой стороны, текущие испытания позволяют, приняв за данность большую эффективность жесткого крепления (она не подвергается сомнению), максимально оценить способность самого кресла защитить ребенка за счет формы, энергопоглощающих материалов, дополнительных элементов боковой защиты и управляемой деформации.
Вообще, разнообразие применяемых методик тестирования отражает концепцию, которой следуют инженеры Britax Roemer в процессе разработки автокресел - "защита на 360 градусов". Т.е. испытывается все и в максимальном разнообразии вариаций. И в угоду идеальному соответствию действующей методике испытаний, будь то обязательная или независимая не приносится в жертву безопасность в каком-либо ином компоненте.
Да, в результате такого подхода, некоторые инновации компании не дают очевидного для постороннего человека эффекта, поскольку являются не "краш-тестовыми". Те же элементы вроде ATS, Secureguard, XP-Pad и т.д. не могут быть адекватно оценены в рамках действующих общепринятых методик испытаний, при этом, увеличивают цену изделия. Но они являются производной от колоссального испытательного опыта компании и их эффективность проверена множеством тестов в более "жизненных" и разнообразных условиях. Задача ставится не просто получить максимум звездочек в известных испытаниях, но реально обеспечить защиту пассажира, когда условия далеки от идеальных, что очень не характерно для большинства современных производителей детских автокресел.
На этом заканчиваю обзор поездки, надеюсь, удалось рассказать что-то интересное ).
От меня лично огромная благодарность как компании Britax Roemer, так и ее Российскому представительству за приглашение, организацию этой поездки и максимальную открытость в демонстрации как процесса производства, так и испытательной лаборатории.